Basic Info.
Model NO.
MD
Transmission Mode
Oil Pump Drive
Control
Two Way Cartridge
Operation Mode
Manual, Semi-Automatic
Type
Gantry Hydraulic Press
Certification
ISO9001, CE
Transport Package
as Required
Specification
CE
Trademark
JUNENG
Origin
China
HS Code
8462919000
Production Capacity
100 Sets/Year
Product Description
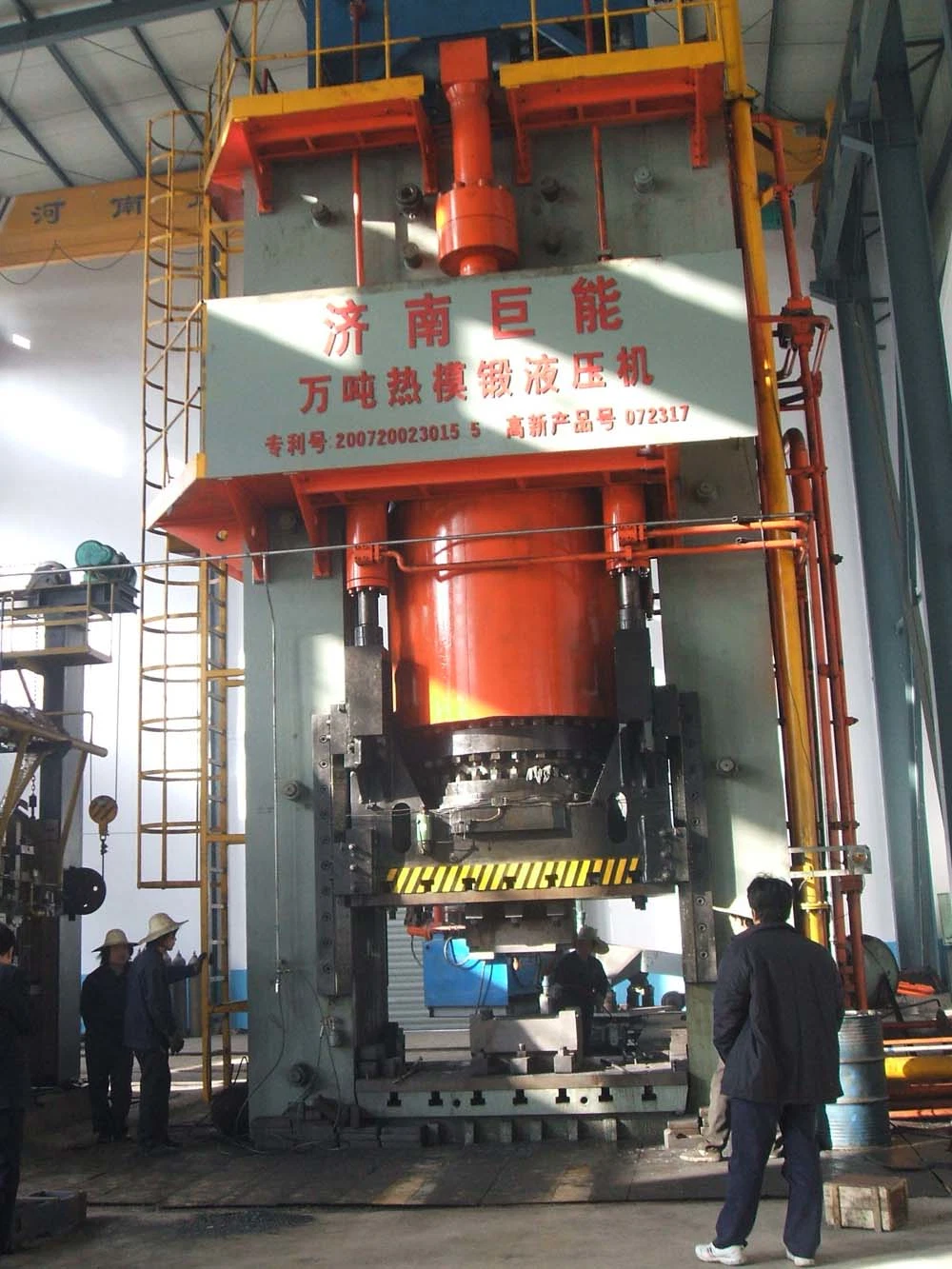
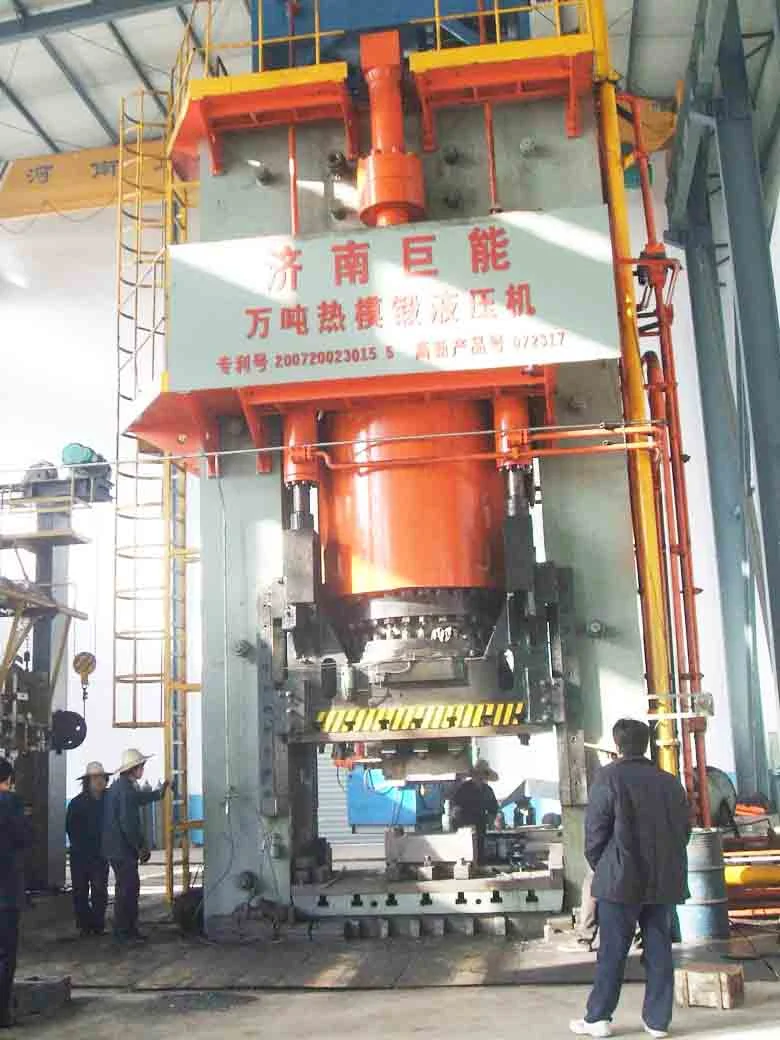
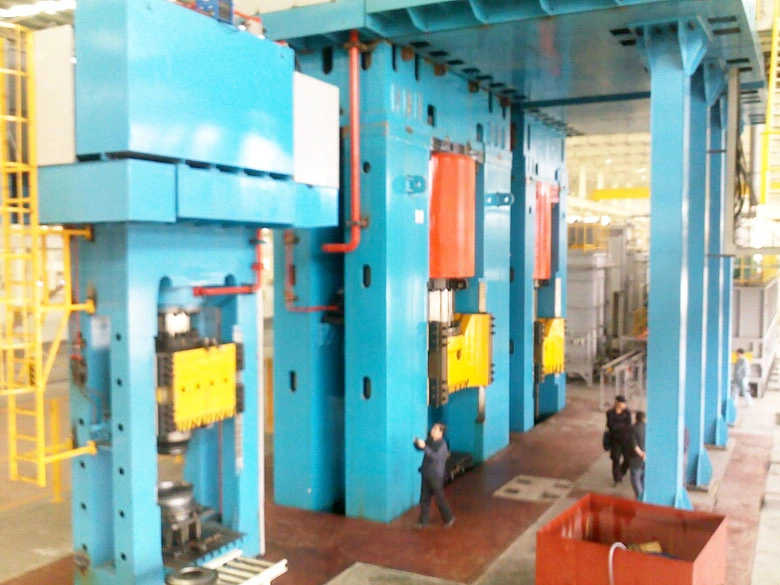
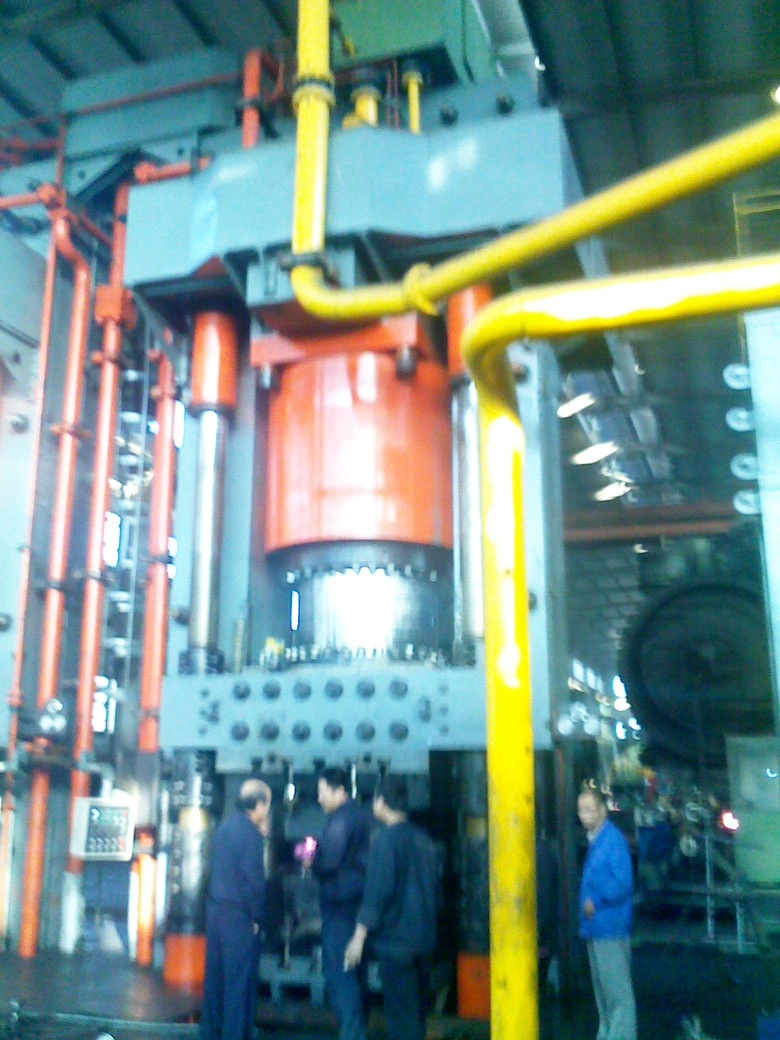
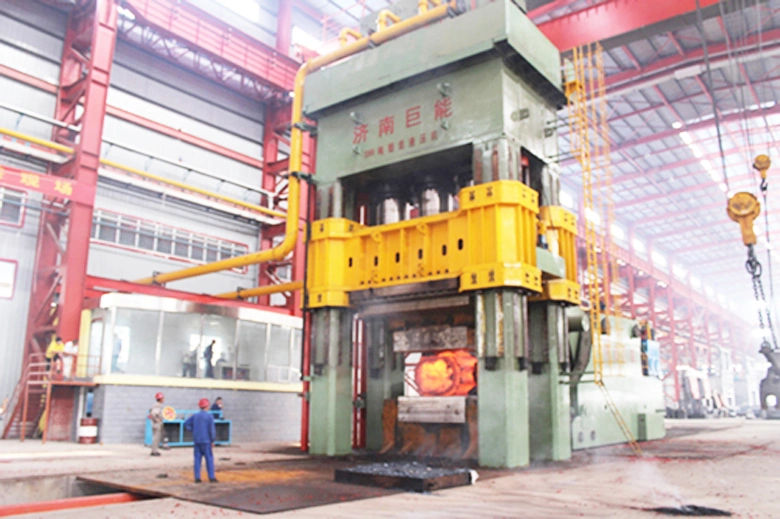
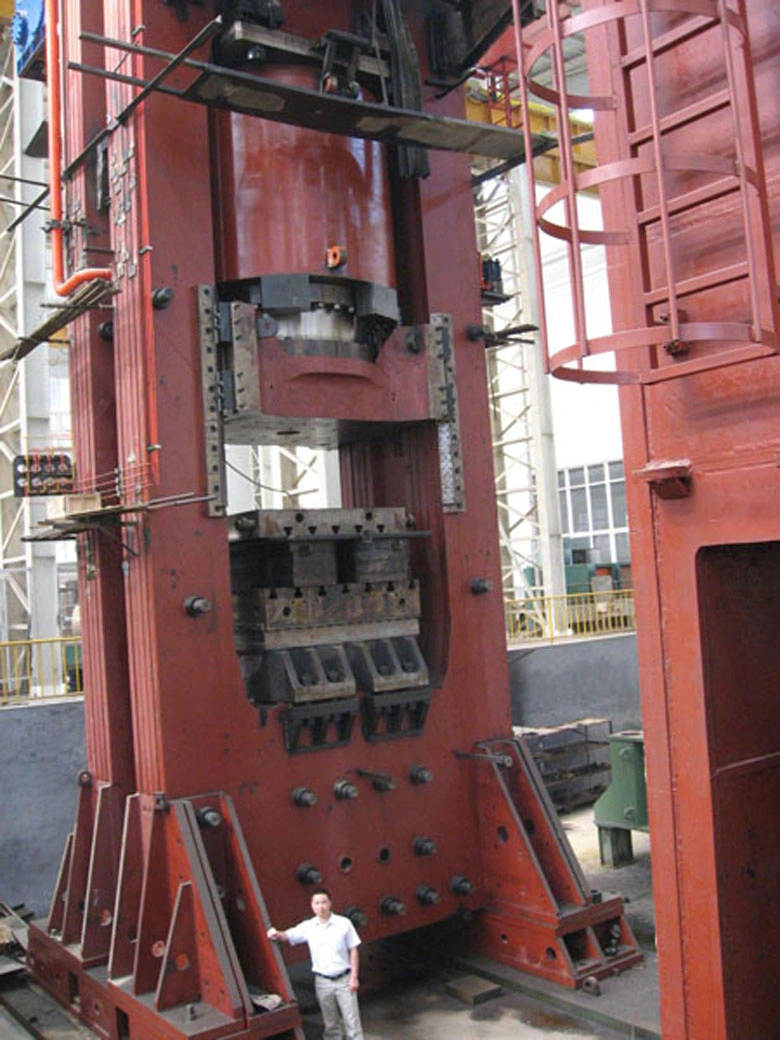
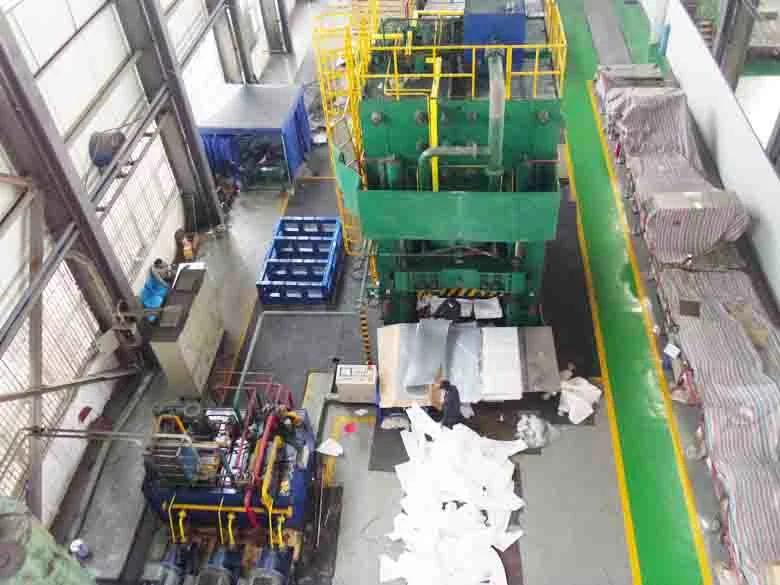
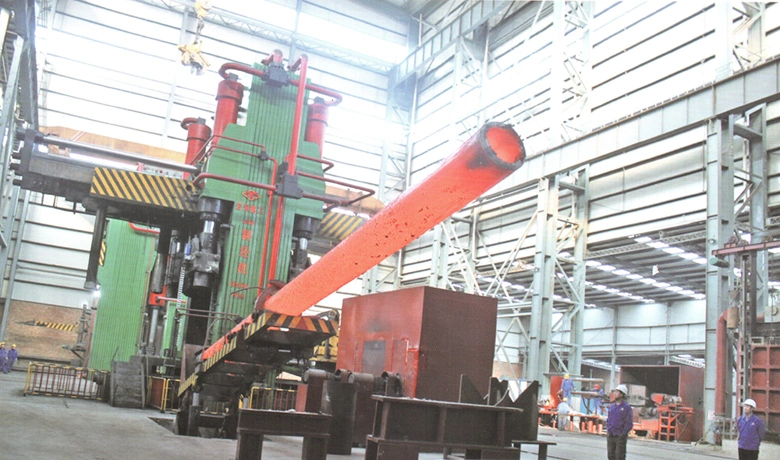
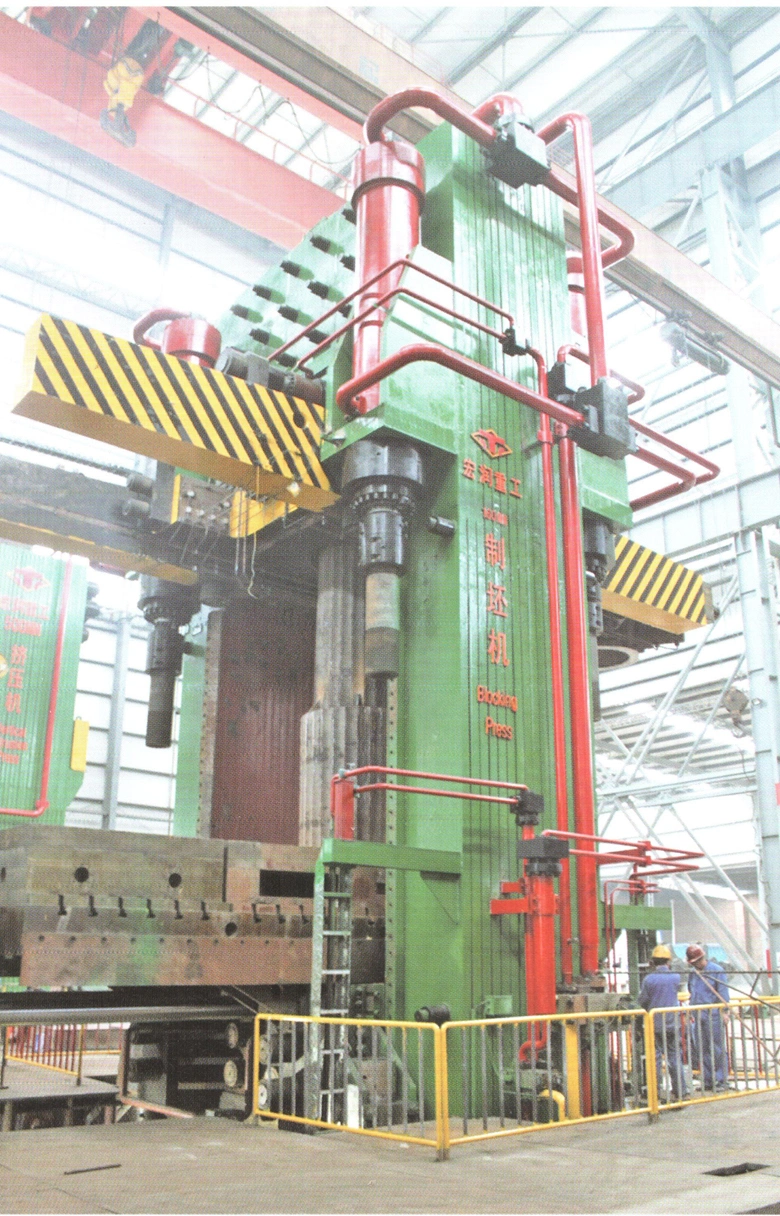
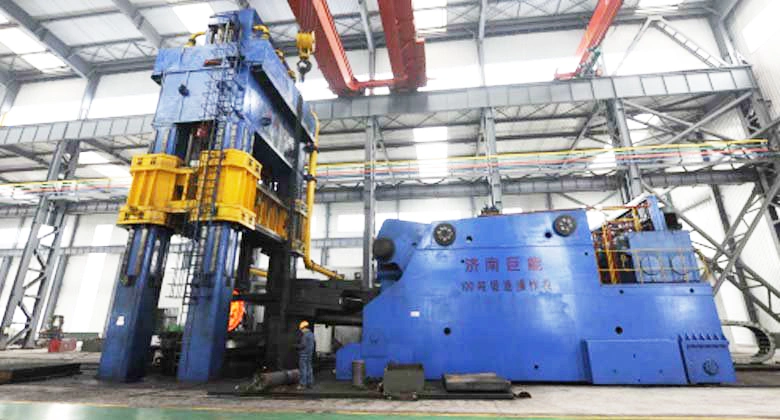
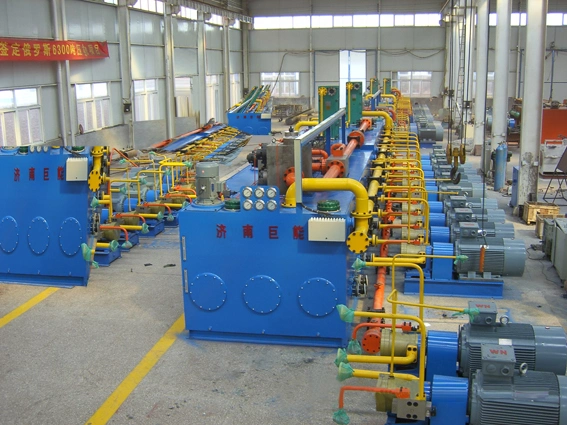
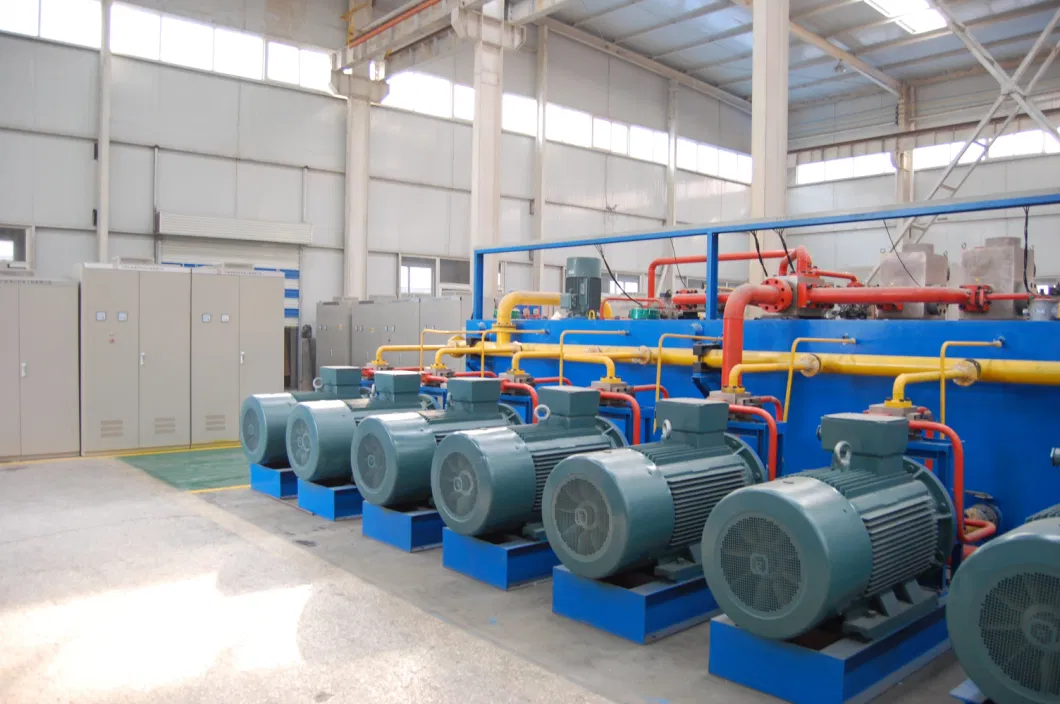
- Function
Hydraulic Device4.1.1 The hydraulic power station installation form: on the ground, as aesthetic as possible and reduce noise.4.1.2 The hydraulic power station is equipped with the oil filtering device. Oil absorbing area and oil return area are separated by the partition. There is a filter on the fueling mouth, ensuring that the oil is clean.4.1.3 The oil temperature control device in the oil cylinderIt uses air conditioner's refrigerating and heating system. The cooling oil filtering system consists of the cooling temperature control device and the filter, guaranteeing the hydraulic oil temperature no more than 50ºC when the hydraulic press works 24 hours continuously.The cooling temperature control device meets the CE certification standards.
2 Oil level is indicated by thermometer.
1 Switching components and pressure gauges that are convenient to observe and adjust for operator are equipped.
2. Oil cylinder liquid-filled system: the prefill valves is set on the top of the press, and the structure is normally closed and self-sucked. When the slider fast moves down, it absorbs to open the prefill valves by dropping down by itself and absorbs the oil from the liquid-filled box.
3.The material of hydraulic pipeline is pressure-resistant seamless steel pipe, and the pipeline joint is connected by flange.
4. The maximum and the minimum oil level, the oil temperature screen and the warning device are equipped on the oil cylinder.
5.Hydraulic Control System
6.The main oil cylinder consists of nine sets of A4VSO250LR oil cylinder that are made by REXROTH; the motor consists of nine sets of china made motor.
7.The working pressure is 31.5MPa.
8.The high pressure main oil cylinder adopts the REXROTH block type axial plunger, normally main pump motor unit is horizontal mounted. The auxiliary oil cylinder chooses china-made high quality product.
9.The hydraulic control system is two way cartridge valve integrated system. It has many advantages, such as small oil resistance, large flow, resistance to pollution, quick response, safe, high reliability, flexible control and convenient repair. All the solenoid valves choose REXROTH products.
10. Two way cartridge valve integrated, reasonable layout, convenient to manufacture, debug and repair.
3. Electrical Device and Electrical Control System
3.1 Electric Device
3.1.1 Equipped with the special control box, set on the ground. The power supply is 480V, 60HZ; the control circuit is 220V. It meets UL508 wire and cable standards; there is 15 percent spare room in the electrical box.
3.1.2 There are power switches, contactor, fuse, control transformer and programmable controller in the electrical control box; the input and output contact metal label should be marked and be the same with the drawing.
3.1.3 Operation table: set on the right-front of the press, the function is to finish each action.
3.2 Electrical Control System
3.2.1 Components of the electrical control system5.2.1.1 Automatic control core components is siemens PLC;
3.2.1.2 All the joints of the electrical controller have the accurate English signs.
3.2.1.3 The main slider has a stroke detection, and the slider position can be arbitrarily set.
3.2.2 Others
3.2.2.1 The electrical control cabinet meets the international standard.
3.2.2.2 The components in the cabinet are set reasonably; all the components are signed correctly, the control lines are marked clearly; there are room for the added components.
3.2.2.3 The control components and the patch panel choose high quality products.
3.3 Processing Specification
3.3.1 Operation mode: inching, manual and continuous automatic. The main control system can be operated by the pedal switch.
3.3.2 Working mode: close die forging forming processing
3.3.3 Others: Pressure and stroke is controlled by labor to realize.
4. Security Protections
4.1 Mechanical Protection:
4.1.1 Signs to electric motor and rotation billets
4.1.2 Zebra crossing alarm on the edge of slider.
4.2 Hydraulic Protection
4.2.1 Main oil pump is protected with retaining valve and overflow valve
4.2.2 Main oil cylinder lower cavity have security overflow valve and double stage supporting plug-in to ensure press slider not slide down as hydraulic press standby.
4.2.3 Cylinder lower cavity has security overflow valve to prevent overpressure.
4.2.4 System overflow valve to prevent overpressure.
4.2.5 Entire system is anti-pipeline injection protected.
4.3 Electric Protection
4.3.1 Electrical motor overloaded protection and short circuit protection use automatic air switch.
4.3.2 Control circuit protection use fuse box.
4.3.3 "Halt urgent" button
4.3.4 Over stroke switch protected
4.3.5 Safe and reliable fittings connected with the earth
4.3.6 Control system components can be halted operation as press broke down
4.3.7 In front of the equipment, photoelectric protection is set.
4.3.8 Electric control system can control slider stroke, press over pressure, over temperature self-locking protection function.
4.4 Operation security measures
4.4.1 Urgency: Press "halt urgent" button
4.4.2 Press operation status light signal display
4.4.3 Security marks: There are zebra lines on the bottom of the slider.
Close die forging press
630t-50000t
Oil hydraulic
Working pressure 25MPa, 31.5MPa, 63MPa, 100MPa
Prestressing frame
Rexroth pump
Special designed cartridge valves
Siemens PLC
ITEM | UNIT | MDYJ | MDYJ | MDYJ | MDYJ | MDYJ | MDYJ | MDYJ |
-630 | -800 | -1250 | -2000 | -3150 | -5000 | -10000 | ||
CAPACITY | KN | 6300 | 8000 | 12500 | 20000 | 31500 | 50000 | 100000 |
WORKING OIL PRESSURE | MPa | 25 | 25 | 25 | 25 | 25 | 25 | 75 |
CAPACITY OF RETURN | KN | 500 | 800 | 1000 | 1250 | 1500 | 2000 | 2000 |
CAPACITY OF PEAK | KN | 500 | 1000 | 1500 | 1500 | 2000 | 2500 | 2500 |
DAYLIGHT | mm | 1200 | 1200 | 1200 | 1200 | 1500 | 1500 | 1500 |
STROKE | mm | 600 | 600 | 600 | 600 | 800 | 1200 | 800 |
SPEED AT APPROACH | mm/s | 200 | 200 | 250 | 250 | 250 | 300 | 100 |
SPEED AT WORK(ADJUSTABLE) | mm/s | 150 | 150 | 100 | 100 | 50 | 3-15 | 3-15 |
RETURN SPEED | mm/s | 200 | 200 | 250 | 250 | 250 | 300 | 100 |
DIMENSION OF SHIFTING TABLE(L-R) | mm | 1000 | 1400 | 1000 | 1000 | 2000 | 2500 | 2500 |
DIMENSION OF SHIFTING TABLE(F-A) | mm | 1000 | 800 | 1250 | 1250 | 1500 | 2000 | 1500 |